Applications and Industries
Education
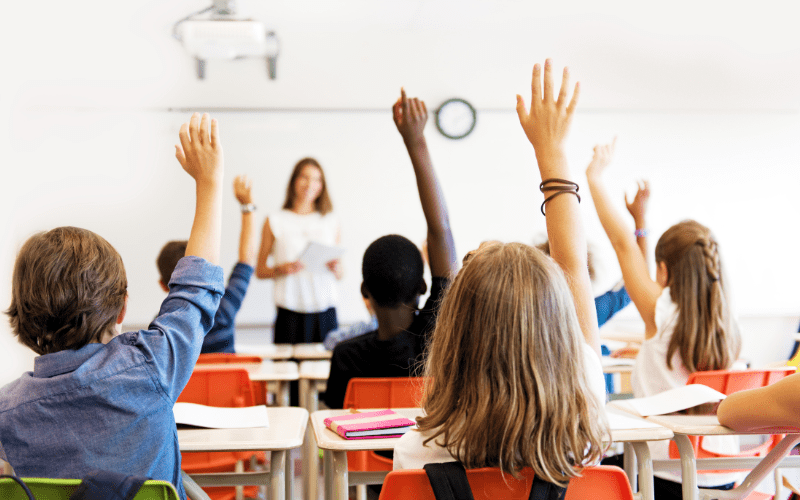
CNC routers, renowned for their versatility, are a staple in universities and schools. They enable the production of a diverse array of 2D and 3D objects from wood, plastics, foam, and various other materials.
Universities and schools worldwide have produced many prototypes using their CNC machines.
The Olympus range and our Pegasus ATC CNC routers are popular in architecture, woodworking, physics and engineering for projects, research, and development.
Opus CNC also specialises in laser cutters for schools. The Oculus range of laser cutters has been installed in schools and universities throughout the UK in many departments.
Furniture Makers
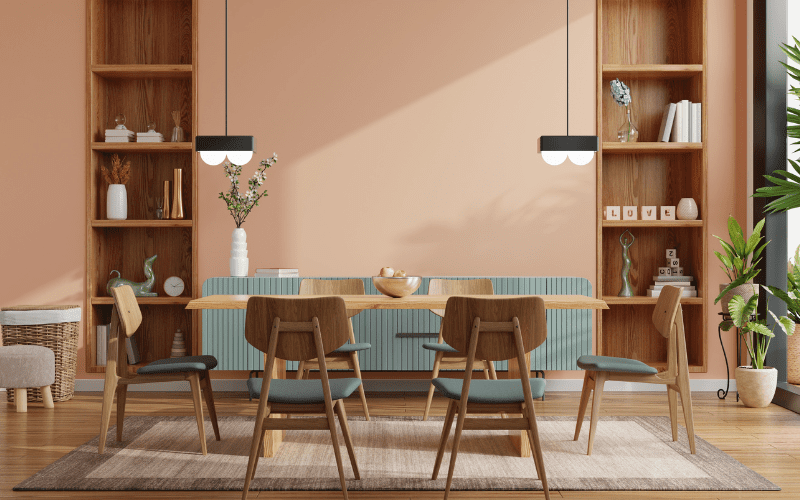
Furniture making is a time-honoured craft that has been passed down through generations. With the advent of technology, furniture making has become more efficient and accurate.
One of the most significant technological advancements in furniture-making is using CNC routers. A CNC router cuts, shapes, and engraves wood, plastic, and metal materials. It uses a rotating cutting tool, such as a router bit or end mill, to remove material from the workpiece.
The VCarve Pro design software guides the cutting tool, allowing precise and accurate cuts.
The Pegasus ATC CNC router is popular among furniture-making customers due to its high-spec and industry-leading build.
Sign Making
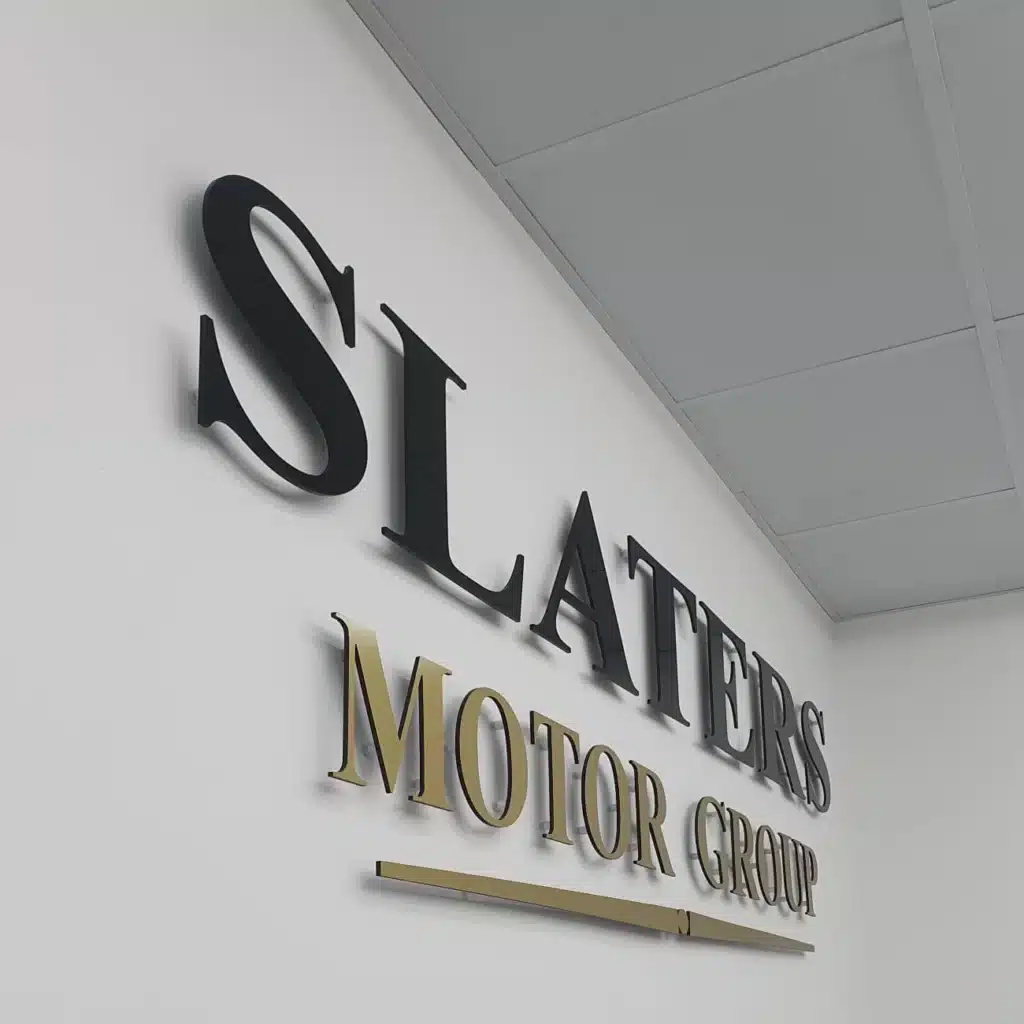
Sign-making with a CNC router is a popular and efficient way to create professional-looking signs for various purposes.
CNC routers are computer-controlled machines that precisely and accurately cut, carve, and engrave multiple materials.
They are often used to create custom signs for businesses, events, and personal projects.
The Olympus range of CNC routers is ideal for any sign company looking to enter the CNC world. Why? The Olympus CNC router is easy to use and suitable for cutting materials such as diBond, acrylic, MDF, and foamex.
Moreover, the Olympus range is not just available in sizes suitable for the signage industry, such as 8’x4′ and 10’x5′, but it is designed specifically to meet the demands of the signage industry, making it a smart investment for any sign company.
Stand Builders
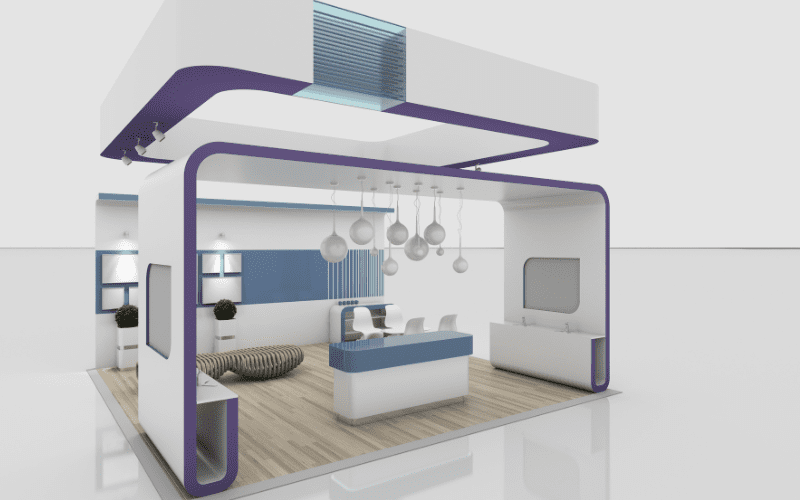
Stand-making with a CNC router is an efficient and cost-effective way to create stands of all shapes and sizes. The precision and speed of the cutting process allow for detailed and complex designs that would be difficult or impossible to achieve by hand.
The result is a beautiful, functional stand made with precision and accuracy. The Oculus flatbed laser, renowned for its ability to cut large-format sheets of acrylic, MDF, and ply with clean cuts, is a versatile tool that enhances the stand-making process.
Our customers, who work in props, sets, and the exhibition building industry, have introduced an Opus CNC router and the Oculus flatbed laser cutting machine.
Campervan Conversions
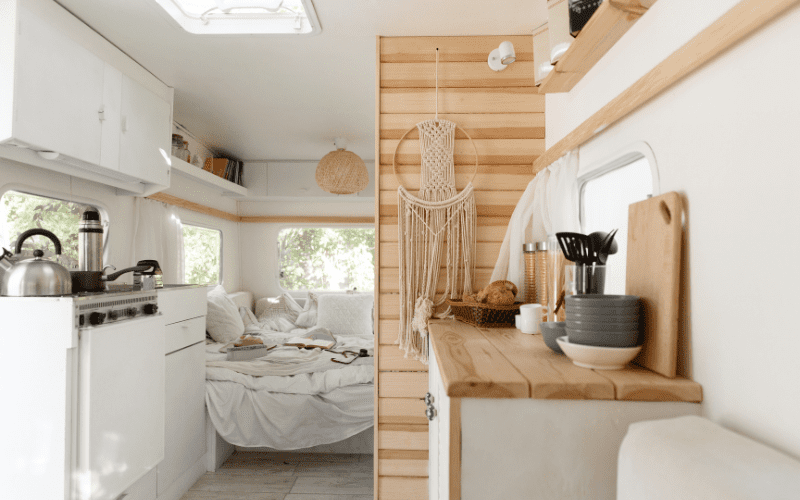
Camper vans have become increasingly popular in recent years as a way to travel and explore the great outdoors in comfort and style. One way to customise and personalise a camper van is by converting it with a CNC router.
One key advantage of using a CNC router for a camper van conversion is the ability to create customised cabinetry and furniture.
Do you currently outsource? Why not bring an Opus CNC router to manufacture your van ply lining or campervan conversion kits? A CNC router can increase production and decrease timescales and costs incurred by outsourcing.Â
Many of our customers in the campervan conversion industry boast that their new Opus CNC router pays for itself within the first year.
The Olympus range of CNC routers is popular among our van conversion customers. There are three options within the Olympus range: the Olympus, the Olympus PRO, and the Olympus ATC.
Marine Applications
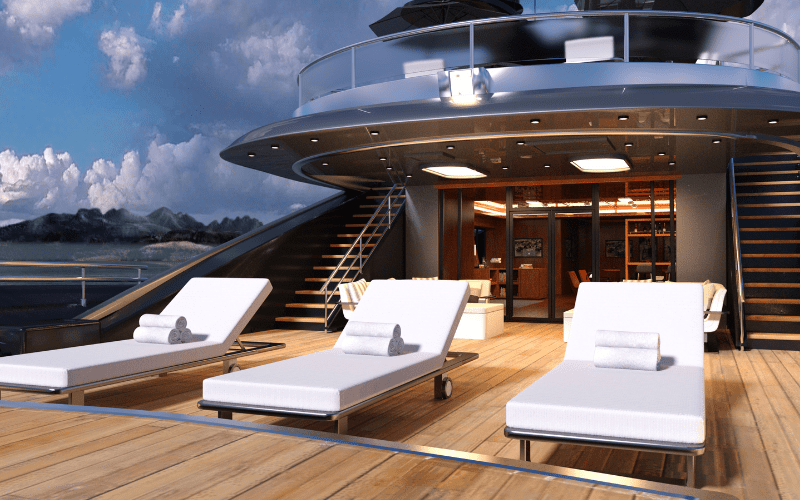
Marine applications for CNC routers are gaining popularity as technology advances and materials become more specialised. CNC routers use a cutting tool to remove material from a workpiece, creating a wide range of precision-cut parts. In the marine industry, these machines are used to create a variety of components, including hulls, decks, and interiors for boats, as well as custom parts for marine equipment.
One of the benefits of using CNC routers in the marine industry is the ability to create precision-cut parts quickly and efficiently. Machines can be programmed to cut a wide range of materials, including wood, composites, and metals, and can be used to accurately create complex shapes and designs.
The full range of Opus CNC routers is suitable for use within marine applications. We have many customers who manufacture boats using one of the Olympus range of CNC routers and some who use the Pegasus ATC CNC router.
Plastic Fabrication
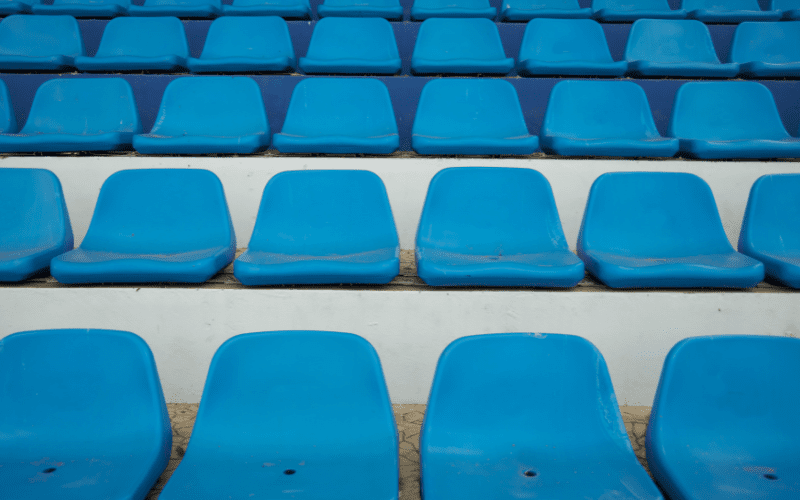
Plastic fabrication with a CNC router is a popular and efficient method for producing various parts and components.
A CNC router is a computer-controlled machine that uses a spinning router bit to cut and shape materials, including plastic. A CNC router makes producing parts with high precision, repeatability, and a smooth finish possible.Â
One key benefit of using a CNC router for plastic fabrication is its versatility. CNC routers can work with many plastics, including acrylic, polycarbonate, PVC, and ABS.
Therefore, a CNC router can fabricate parts for various applications, including automotive, medical, aerospace, and consumer products.
Metal Fabrication
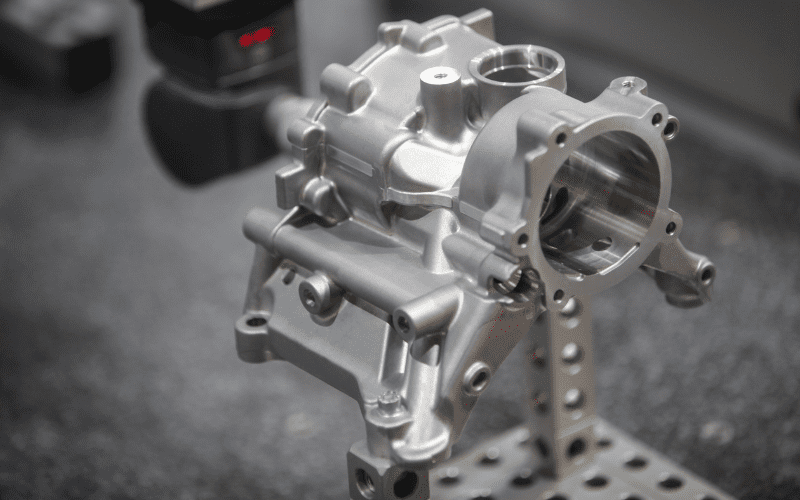
Metal fabrication creates structures, parts, and components through cutting, bending, and assembling. The CNC router is one of the most versatile and efficient tools in metal fabrication today.
A CNC router is a machine that uses a computer program to control the movement of a cutting tool. This allows for precise and accurate cutting of various materials, including metal. The machine uses cutting tools such as end mills and drills, which can easily cut through metal.
One of the main advantages of using a CNC router for metal fabrication is its precision and accuracy. Unlike traditional metal fabrication methods, such as manual cutting or stamping, a CNC router can cut metal within a fraction of a millimetre, ensuring that all parts and components are consistent and perfectly fit.
Aviation Industry
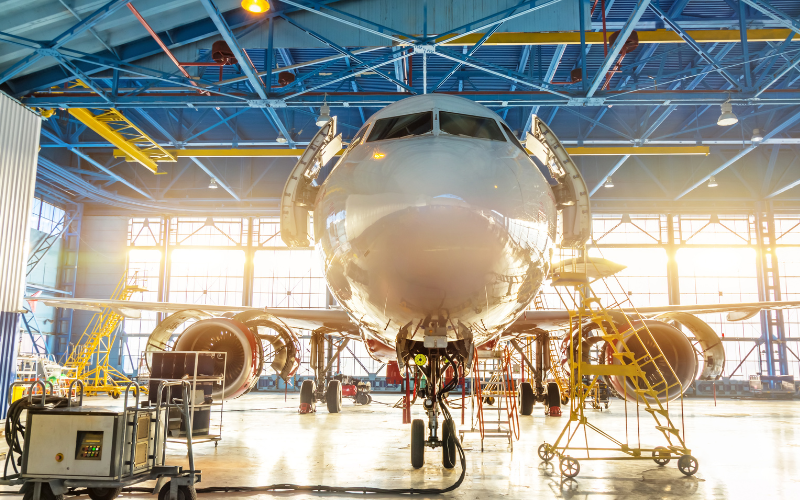
With the ever-growing possibilities of what creations can be made with a CNC router, you will not be surprised to find that the aircraft industry uses them to fabricate various components and parts for manufacturing and maintenance.Â
With a CNC router, not only can they cut out a variety of materials used on the composite structures but, with the precision of the cutting itself, manufacture the instruments used to fly the aircraft, such as the switches and displays.Â
The Pegasus ATC CNC router is popular among aviation customers due to its intricate design capabilities, industry-leading build and feature-packed control system.
Sports Industry
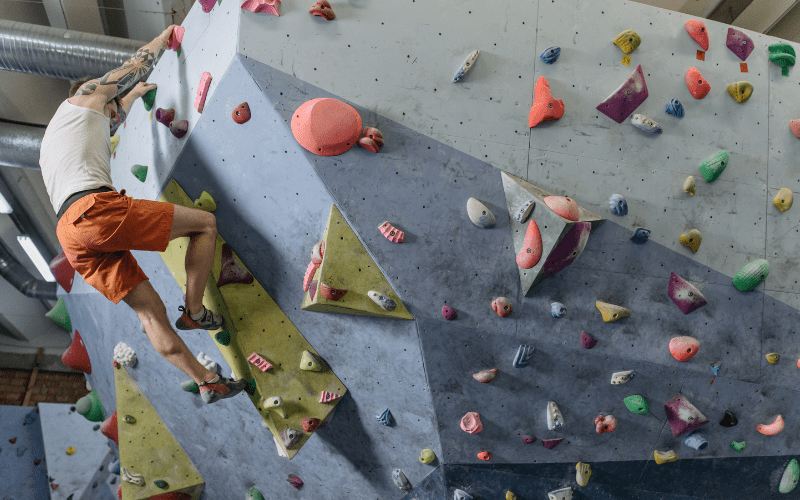
Our state-of-the-art machines offer many benefits, making them invaluable tools for enhancing various sporting activities. From crafting custom equipment and gear to creating intricate training aids and sports facility enhancements, our CNC routers and laser cutters empower athletes, coaches, and sports enthusiasts alike to unlock their full potential.
Our CNC routers ensure unparalleled precision and consistency in sports equipment manufacturing, resulting in high-performance gear that meets athletes’ exacting demands.
Whether it’s crafting flawless snowboards, ergonomic golf club grips, or lightweight bicycle frames, our machines guarantee exceptional quality and durability, enhancing athletes’ performance across the board.
Crafters
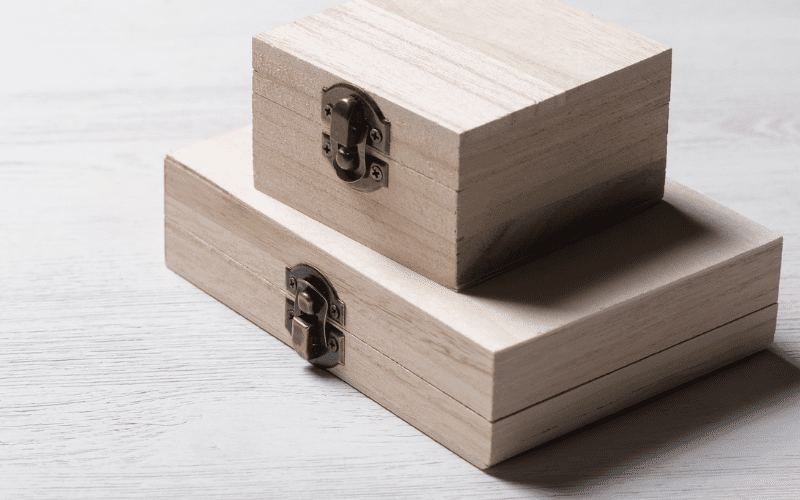
CNC routers and laser cutters are invaluable for crafters. They offer unmatched precision, versatility, and time efficiency to elevate their creative projects.
With CNC routers and laser cutters, crafters can effortlessly work with a variety of materials, customizing designs to suit their unique vision. The automation and speed of these machines significantly reduce crafting time, ensuring consistent and reproducible results.
Complex and intricate designs that were once challenging become easily achievable, inspiring crafters to explore new possibilities. Moreover, these tools optimize material usage, minimizing waste and environmental impact.
Whether crafting for pleasure or running a business, CNC routers and laser cutters empower crafters to unleash their creativity and take their projects to new heights, making them indispensable assets in crafting.
Cabinet Making

CNC routers and laser cutters are indispensable tools for cabinet makers, revolutionising the woodworking industry with their myriad benefits. These advanced machines offer precision and accuracy beyond manual capabilities, ensuring flawless cuts and intricate designs for cabinet components.
With CNC routers, cabinet makers can automate the production process, significantly reducing fabrication time while maintaining consistent quality across multiple units. Laser cutters, on the other hand, excel at engraving, etching, and creating intricate details on cabinet surfaces, elevating the aesthetics of the final product. These tools also enable cabinet makers to work with various materials, from solid wood to plywood and MDF, expanding their creative possibilities.
Additionally, CNC routers and laser cutters facilitate customisation, allowing cabinet makers to cater to specific client needs and preferences, enhancing customer satisfaction. By streamlining production, improving precision, and enabling artistic detailing, CNC routers and laser cutters become invaluable assets that empower cabinet makers to craft top-notch cabinetry efficiently and creatively.
Education
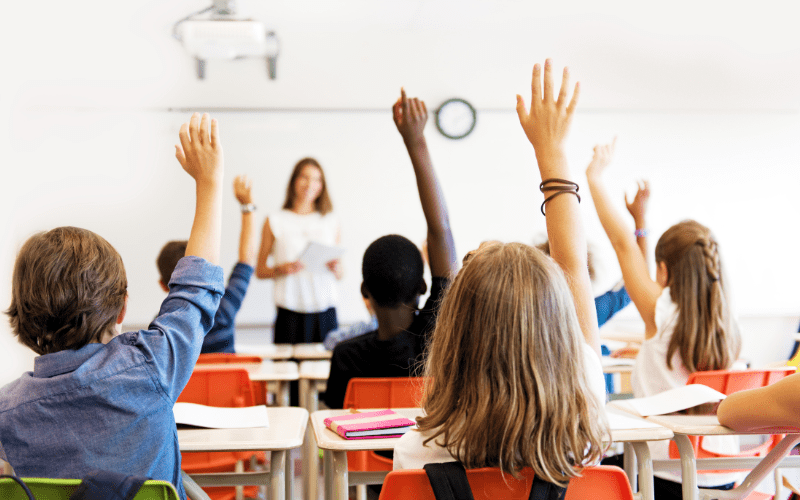
CNC routers, renowned for their versatility, are a staple in universities and schools. They enable the production of a diverse array of 2D and 3D objects from wood, plastics, foam, and various other materials.
Universities and schools worldwide have produced many prototypes using their CNC machines.
The Olympus range and our Pegasus ATC CNC routers are popular in architecture, woodworking, physics and engineering for projects, research, and development.
Opus CNC also specialises in laser cutters for schools. The Oculus range of laser cutters has been installed in schools and universities throughout the UK in many departments.
Furniture Makers
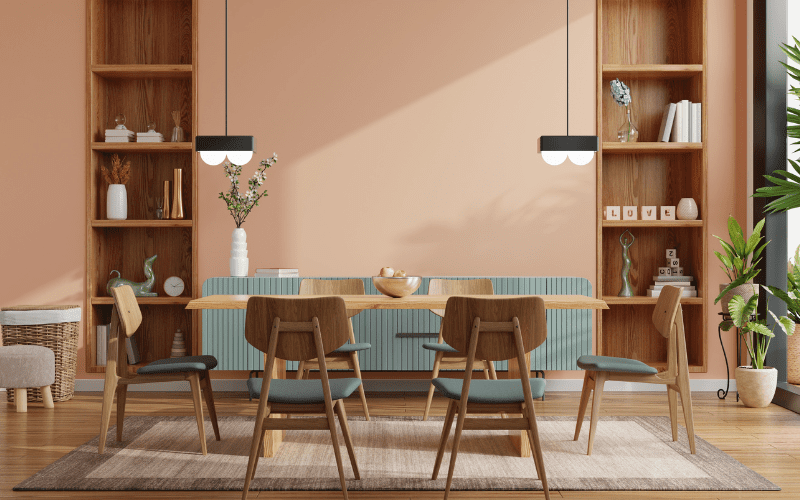
Furniture making is a time-honoured craft that has been passed down through generations. With the advent of technology, furniture making has become more efficient and accurate.
One of the most significant technological advancements in furniture-making is using CNC routers. A CNC router cuts, shapes, and engraves wood, plastic, and metal materials. It uses a rotating cutting tool, such as a router bit or end mill, to remove material from the workpiece.
The VCarve Pro design software guides the cutting tool, allowing precise and accurate cuts.
The Pegasus ATC CNC router is popular among furniture-making customers due to its high-spec and industry-leading build.
Sign Making
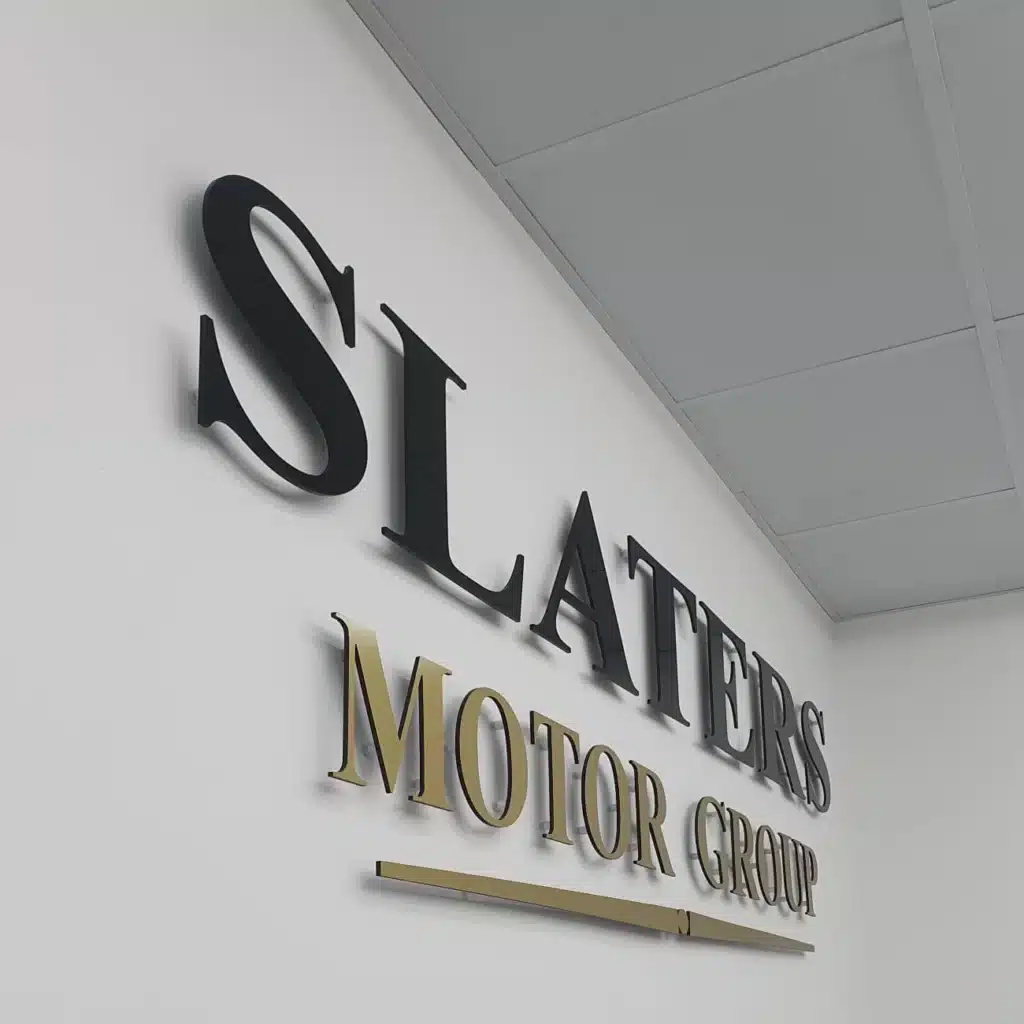
Sign-making with a CNC router is a popular and efficient way to create professional-looking signs for various purposes.
CNC routers are computer-controlled machines that precisely and accurately cut, carve, and engrave multiple materials.
They are often used to create custom signs for businesses, events, and personal projects.
The Olympus range of CNC routers is ideal for any sign company looking to enter the CNC world. Why? The Olympus CNC router is easy to use and suitable for cutting materials such as diBond, acrylic, MDF, and foamex.
Moreover, the Olympus range is not just available in sizes suitable for the signage industry, such as 8’x4′ and 10’x5′, but it is designed specifically to meet the demands of the signage industry, making it a smart investment for any sign company.
Stand Builders
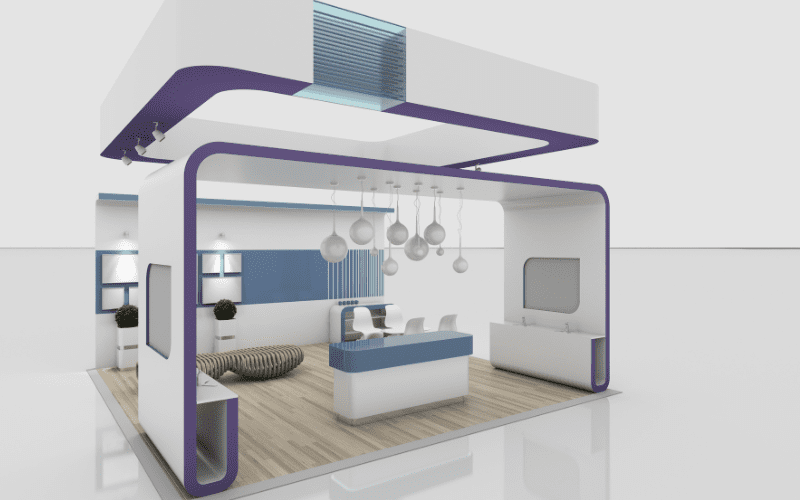
Stand-making with a CNC router is an efficient and cost-effective way to create stands of all shapes and sizes. The precision and speed of the cutting process allow for detailed and complex designs that would be difficult or impossible to achieve by hand.
The result is a beautiful, functional stand made with precision and accuracy. The Oculus flatbed laser, renowned for its ability to cut large-format sheets of acrylic, MDF, and ply with clean cuts, is a versatile tool that enhances the stand-making process.
Our customers, who work in props, sets, and the exhibition building industry, have introduced an Opus CNC router and the Oculus flatbed laser cutting machine.
Campervan Conversions
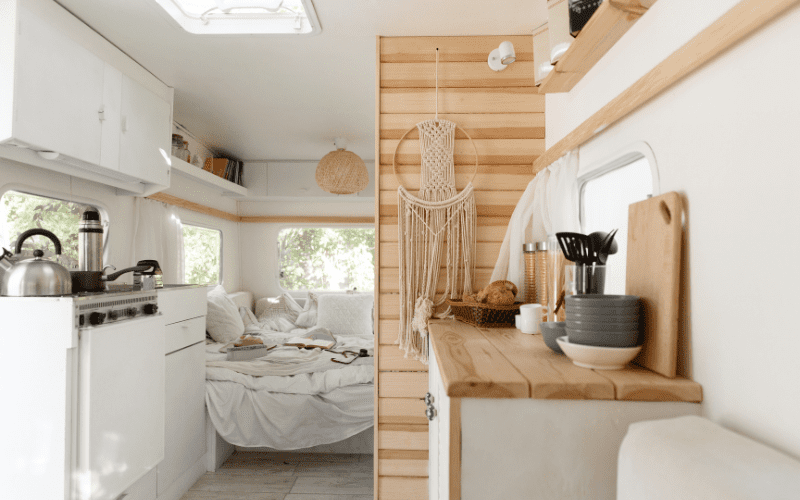
Camper vans have become increasingly popular in recent years as a way to travel and explore the great outdoors in comfort and style. One way to customise and personalise a camper van is by converting it with a CNC router.
One key advantage of using a CNC router for a camper van conversion is the ability to create customised cabinetry and furniture.
Do you currently outsource? Why not bring an Opus CNC router to manufacture your van ply lining or campervan conversion kits? A CNC router can increase production and decrease timescales and costs incurred by outsourcing.Â
Many of our customers in the campervan conversion industry boast that their new Opus CNC router pays for itself within the first year.
The Olympus range of CNC routers is popular among our van conversion customers. There are three options within the Olympus range: the Olympus, the Olympus PRO, and the Olympus ATC.
Marine Applications
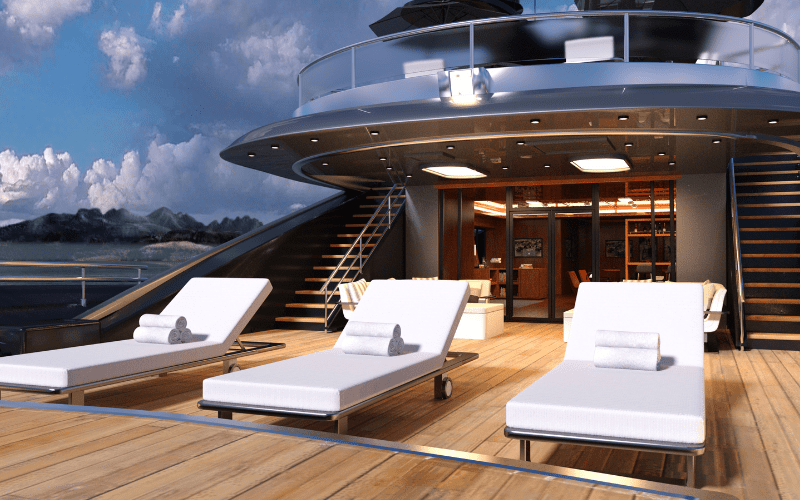
Marine applications for CNC routers are gaining popularity as technology advances and materials become more specialised. CNC routers use a cutting tool to remove material from a workpiece, creating a wide range of precision-cut parts. In the marine industry, these machines are used to create a variety of components, including hulls, decks, and interiors for boats, as well as custom parts for marine equipment.
One of the benefits of using CNC routers in the marine industry is the ability to create precision-cut parts quickly and efficiently. Machines can be programmed to cut a wide range of materials, including wood, composites, and metals, and can be used to accurately create complex shapes and designs.
The full range of Opus CNC routers is suitable for use within marine applications. We have many customers who manufacture boats using one of the Olympus range of CNC routers and some who use the Pegasus ATC CNC router.
Plastic Fabrication
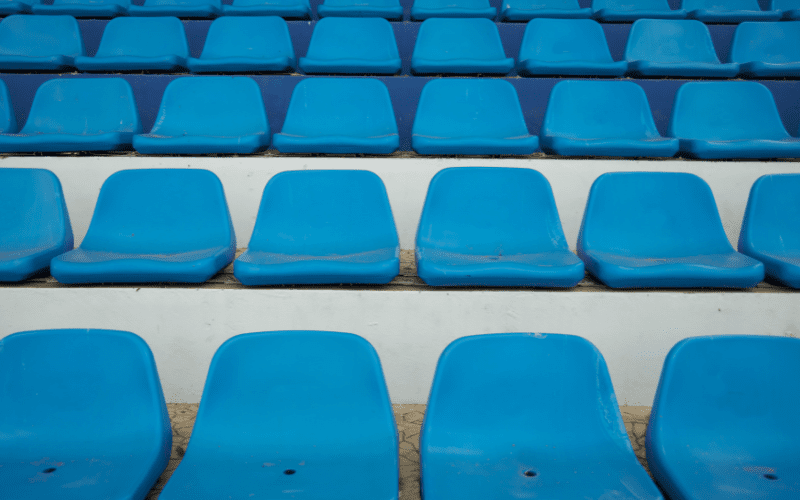
Plastic fabrication with a CNC router is a popular and efficient method for producing various parts and components.
A CNC router is a computer-controlled machine that uses a spinning router bit to cut and shape materials, including plastic. A CNC router makes producing parts with high precision, repeatability, and a smooth finish possible.Â
One key benefit of using a CNC router for plastic fabrication is its versatility. CNC routers can work with many plastics, including acrylic, polycarbonate, PVC, and ABS.
Therefore, a CNC router can fabricate parts for various applications, including automotive, medical, aerospace, and consumer products.
Metal Fabrication
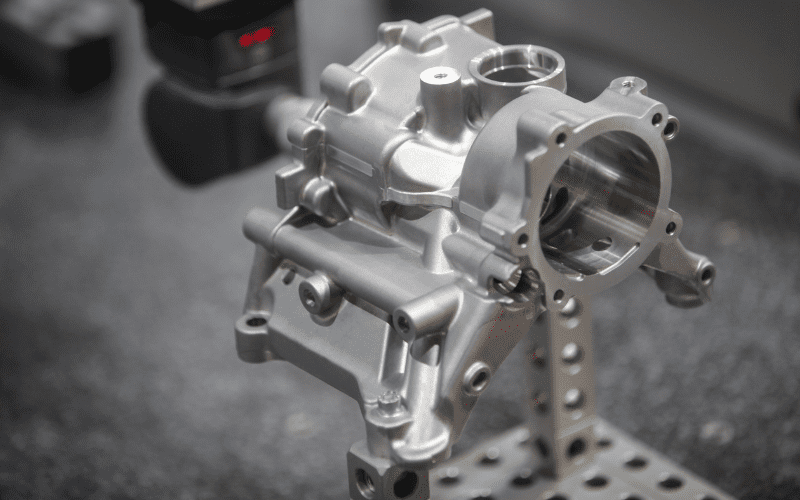
Metal fabrication creates structures, parts, and components through cutting, bending, and assembling. The CNC router is one of the most versatile and efficient tools in metal fabrication today.
A CNC router is a machine that uses a computer program to control the movement of a cutting tool. This allows for precise and accurate cutting of various materials, including metal. The machine uses cutting tools such as end mills and drills, which can easily cut through metal.
One of the main advantages of using a CNC router for metal fabrication is its precision and accuracy. Unlike traditional metal fabrication methods, such as manual cutting or stamping, a CNC router can cut metal within a fraction of a millimetre, ensuring that all parts and components are consistent and perfectly fit.
Aviation Industry
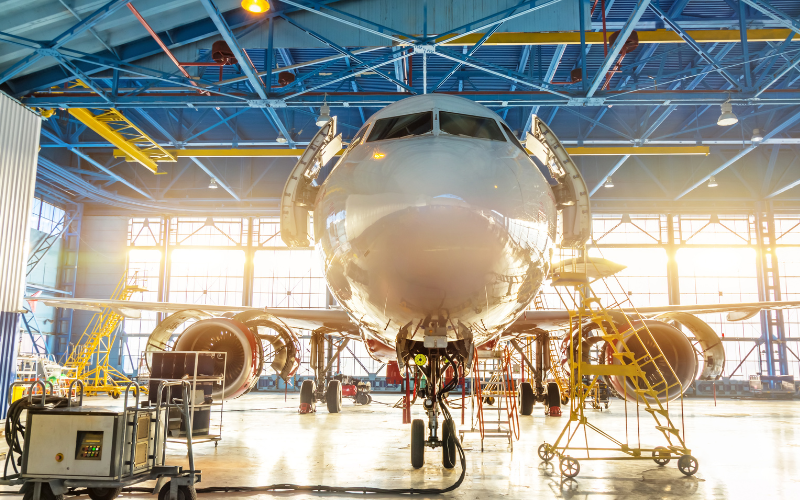
With the ever-growing possibilities of what creations can be made with a CNC router, you will not be surprised to find that the aircraft industry uses them to fabricate various components and parts for manufacturing and maintenance.Â
With a CNC router, not only can they cut out a variety of materials used on the composite structures but, with the precision of the cutting itself, manufacture the instruments used to fly the aircraft, such as the switches and displays.Â
The Pegasus ATC CNC router is popular among aviation customers due to its intricate design capabilities, industry-leading build and feature-packed control system.
Sports Industry
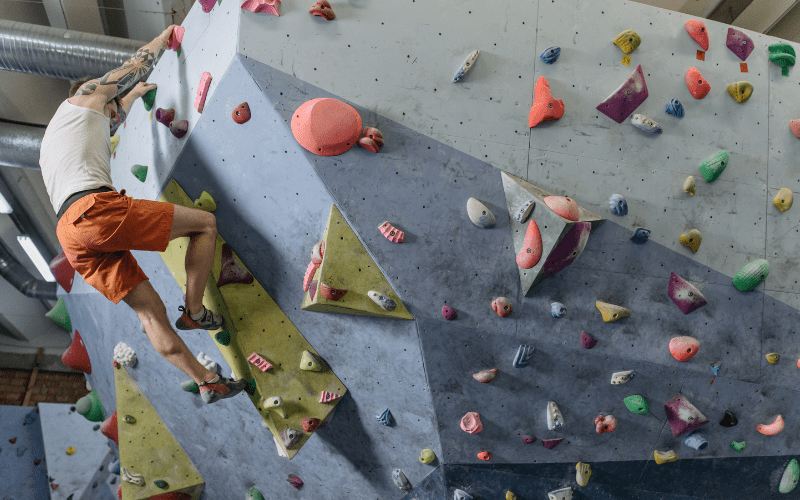
Our state-of-the-art machines offer many benefits, making them invaluable tools for enhancing various sporting activities. From crafting custom equipment and gear to creating intricate training aids and sports facility enhancements, our CNC routers and laser cutters empower athletes, coaches, and sports enthusiasts alike to unlock their full potential.
Our CNC routers ensure unparalleled precision and consistency in sports equipment manufacturing, resulting in high-performance gear that meets athletes’ exacting demands.
Whether it’s crafting flawless snowboards, ergonomic golf club grips, or lightweight bicycle frames, our machines guarantee exceptional quality and durability, enhancing athletes’ performance across the board.
Crafters
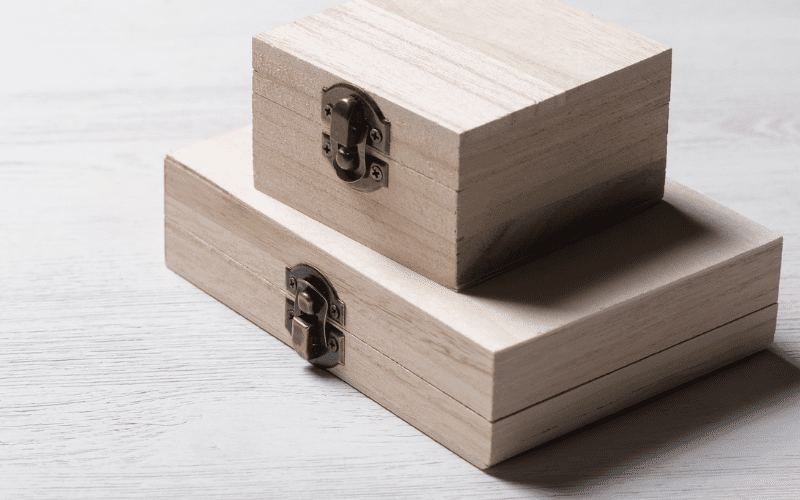
CNC routers and laser cutters are invaluable for crafters. They offer unmatched precision, versatility, and time efficiency to elevate their creative projects.
With CNC routers and laser cutters, crafters can effortlessly work with a variety of materials, customizing designs to suit their unique vision. The automation and speed of these machines significantly reduce crafting time, ensuring consistent and reproducible results.
Complex and intricate designs that were once challenging become easily achievable, inspiring crafters to explore new possibilities. Moreover, these tools optimize material usage, minimizing waste and environmental impact.
Whether crafting for pleasure or running a business, CNC routers and laser cutters empower crafters to unleash their creativity and take their projects to new heights, making them indispensable assets in crafting.
Cabinet Making

CNC routers and laser cutters are indispensable tools for cabinet makers, revolutionising the woodworking industry with their myriad benefits. These advanced machines offer precision and accuracy beyond manual capabilities, ensuring flawless cuts and intricate designs for cabinet components.
With CNC routers, cabinet makers can automate the production process, significantly reducing fabrication time while maintaining consistent quality across multiple units. Laser cutters, on the other hand, excel at engraving, etching, and creating intricate details on cabinet surfaces, elevating the aesthetics of the final product. These tools also enable cabinet makers to work with various materials, from solid wood to plywood and MDF, expanding their creative possibilities.
Additionally, CNC routers and laser cutters facilitate customisation, allowing cabinet makers to cater to specific client needs and preferences, enhancing customer satisfaction. By streamlining production, improving precision, and enabling artistic detailing, CNC routers and laser cutters become invaluable assets that empower cabinet makers to craft top-notch cabinetry efficiently and creatively.